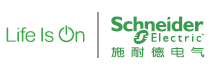
在全球应对气候变化的进程中,各国陆续出台对应举措,中国也提出了“3060”双碳目标,都在朝着可持续发展转型。其中作为“碳大户”的制造业更是迫切需要脱碳加速度。
近期,施耐德电气携手麻省理工科技评论联合发布了以《设备管理与可持续发展》为题的报告。报告指出,制造企业正在携手推动行业可持续发展进程,并设定基于供应链碳排放可见性的长期目标。
为了积极推动脱碳,制造企业正在采取多样化的举措。要实现这一目标,根据施耐德电气可持续研究院的测算,未来能源供给端要承担45%的脱碳,而能源需求端要承担55%的脱碳。
点击查看施耐德电气全球执行副总裁与MIT高级分析师的深度解读👆
那在能源需求侧有哪些重点关注和趋势呢?
互联互通“洞见症结”
提高能效可见性,深入洞见
通过数字化技术实现机械设备自动化、监控和分析制造过程的功能,通常称为“工业4.0”。在4.0阶段,制造业的领军企业正在重塑制造流程,改进能源效率并优化材料使用。在制造业工厂的生产和运营环节中,每个环节的能耗都会影响整体效率和碳排放总量。要扫除可持续制造之路上的障碍,关键是通过数字化连接和数据分析,让设备情况“看得见”。
通过采用传感器和绩效管理工具追踪能耗及碳排,企业可以降低维护成本,实现更高水平的设备管理和绩效管理,有助于企业提升设备性能,减少废弃物,降低产品制造过程中碳密集型资源的使用量。
技术加持“灵活多变”
实现流程精益化、产线模块化
技术这张“王牌”对于制造业来说至关重要,它能帮助构建更完善的预测流程,以提升流程的精益化及模块化水平。这不仅有助于实现更精确的校准,为原材料、产线和流程的投入提供依据,还可以更好地预测数据,使生产商可以从一开始就设计出更可持续的制造流程。
美国的一家企业就利用虚拟技术和分析工具开发了各种数字模型,利用预测工具,预先在虚拟现实场景中,对可持续的生产模型进行压力测试后,再投入实际生产线。这不仅能提升产品质量,还有助于改进设备功能。
循环经济“绿色降本”
产品的全生命周期设计
为加快实现“循环经济”, 制造业领军企业需要重塑制造流程,在可持续性设计制造原则下,企业需要面向材料管理制定长期的业务发展计划。通过建造新的设施来拆解现有产品,以更好地利用备件和总拥有成本(TCO)模型,精简产品设计流程,增加可持续性投入,甚至缩短机械密集型产品的使用寿命,从而更好地利用电气效率的迭代创新成果。
法国的一家汽车制造商就正在投建专门拆卸旧卡车的新工厂,计划将拆下的零件再利用,这与整车一同报废相比,能耗自然更小。
此次研究成果表明,制造业的可持续发展正在从偶然走向必然。当前,高效的设备管理与明确的绿色发展目标正推动制造业迈向高效脱碳之路。然而,想要实现全球气候目标,制造业仍需争分夺秒,持续优化数据和数字技术的使用方式,加速自身脱碳进程。
——Frederic Godemel
施耐德电气全球执行副总裁
电力系统与服务业务负责人
可持续发展一直是施家的宗旨以及业务的核心。在加速自身业务可持续发展的同时,施家持续开拓创新,为赋能企业最大化利用能源和资源而努力。不仅建立了回收、翻新、再利用的大型循环模型,并在咨询、现代化改造和维护业务部门新增了2,500个绿色职位。面对气候变化挑战,施家还将携手更多企业,持续发现节能新机会!