当GM公司于2002年宣布要建立一个全球通用标准的传动平台时,他的目标非常明确:满足生产快速调整的需要、降低成本并且简化安装和维护工作。这个解决方案要既能够用于新建工厂,也能够用于现有工厂的改造升级。这个解决方案所选择的技术据说在GM公司全球各地的工厂里都获得了胜利。 对于GM公司控制、传动、机器人和焊接集团的高级制造项目工程师Hans Rodgers来说,由SEW-Eurodrive公司开发的一体化传动控制系统的美妙之处在于——简单。这个系统由高度模件化的单元组成,包括一体化的传动马达、驱动以及一个独立的、由一个安全继电器供电的24V直流安全回路。无需端子接线和编程工作,这样就使现场的电气技术人员只需进行简单、快捷的安装工作即可,使他们能够使用标准的传动模件。 SEW公司的传动控制系统为组装工厂带来了更强的灵活性,使得生产线可以根据不同的汽车车体在短短几天的时间里完成改变,而不是像以前那样需要花费几个月时间。SEW公司的传动控制系统还使GM公司可以实现显著降低工程费用和安装费用的目标。节约的效果通过使用较少的部件、较少的接线和维护工作来实现,再加上消灭了讨厌的紧急停车,这样可以减少停工的时间。在一个工厂中,每个驱动系统可以节省多达1000美元。
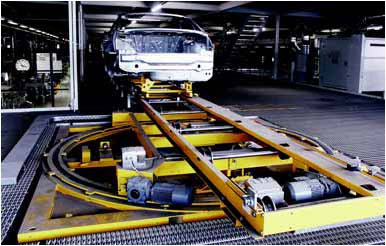 “我们在全球各地生产类似的车体,”Rodgers解释说,“但是,在很多情况下当地的工厂都没有把其它工厂的经验利用起来,而是在设计汽车传送设备时不断的重复别处已经走过的弯路。现在我们有了一套设计和实施都非常简单和便宜的控制系统,无论工厂位于北美洲或南美洲、欧洲或者亚洲。这就是我们称之为标准化柔性系统的东西。” 采用这种柔性系统,GM公司只用很少几种不同的传动模件就可以适应公司的大多数汽车生产要求。使用通用制造设备架构的能力对于减少制造过程中的不必要支出是非常关键的。 分散控制是关键 简单化还体现在工程设计施工当中:SEW公司的控制系统是分散化的,采用一个一体化的、安装在传动模件上的驱动和传动马达来实现。这种方式明显减少了现场接线。除了分散化的控制系统以外,新的即插即用SEW模件(被称为“连接器化”的单元)完全取消了现场接线端子。即使是在中国这样的劳动力廉价地区,GM公司的工程师也满怀信心的认为连接器将会明显节省人工费用。另外,这种改变还最大限度的减少了接线错误。在任何制造业工厂里,接线错误都是一再发生的、造成工厂开车延误的原因之一。 双列直插封装(DIP)开关取代了软件对驱动设备进行组态。这种方法已经被证明是一种成本较低的设计,它不需要进行软件编程以及相关的培训。键盘、手提电脑和其它附加设备也不再是必需品,这使得有关人员的安装工作和维护工作更加容易。“有时低技术反而是最好的技术,”SEW公司的机动车分部经理Tom Curtin说道。“一旦你搞清楚驱动设备应该怎样控制马达,你就不需要对每个单独的驱动设备进行编程了。对于SEW公司制造的驱动设备和马达来说,用DIP开关可以很容易的使马达控制实现标准化。” 并且集成在驱动设备里边的24伏安全停车回路替代了传统的安全硬件组件。这种设计方式的组合有助于消除现场工程设计和安装变更,使得建立一种全球通用的平台成为可能。 取消了昂贵的接触器 SEW公司的设计使得GM公司可以不再需要使用价格昂贵的安全接触器——在传统的安全设计里这是必不可少的——却不会对工人的安全带来影响。作为替代,采用了一种将安全功能与用于控制驱动设备和马达的线电压电源分离开来的低压方法,这样可以实现一个24伏直流安全停车(EN954-1类别3)。在需要时,这种方法能够切断24伏直流安全供电,以便防止变频驱动设备里边的功率晶体管着火,使得被驱动设备所控制的马达处于一种不能产生扭矩的状态——虽然480伏电源并未断开。 因为安全停车是由一个单独的回路实现的,所以它可以使传动运动停止而不必切断控制系统和驱动设备的电源。对于终端用户来说,最重要的是:当安全条件重新具备以后,能够把传动系统迅速的重新开动起来。如果采用传统的在线安装设计,当安全停车发生时,整个驱动回路可能都会从主控制器上被断开。在一次紧急停车之后,必须非常小心的跟踪重新恢复电源的顺序,以便防止对驱动设备造成损害。快速的关闭电源和打开电源是非常危险的,而且会缩短驱动设备的寿命。 “GM公司想要一种标准的安全架构,这样如果一个部件失效了、一个紧急停车按钮被按下了或者一个光帘被触碰到了就可以保护员工免受安全威胁,”Curtin解释说。“我们的安全控制并不仅仅是适合于这种运行模式,它使GM公司可以决定什么样的事件将会触发一次安全停车。GM公司已经在这方面节省了数以百万计的美元。一个典型的工厂会用到上千甚至更多的安全接触器。我们现在已经能够使用一种更加简单、更加便宜的设计来把这方面的费用降低至少60%。” 目前已经有超过5000套SEW公司的新的传动控制系统安装在GM公司在全世界的工厂里边,Curtin高度赞扬了GM公司的技术规划和超前的思维。“由于帮助GM公司进行全球工厂改变所遇到的困难,我们得到了GM公司的感谢,”他说道,“他们分步骤的进行技术改变,就像爬楼梯一样。他们明白对于当地的工厂来说,改变是多么困难。因此他们采用了一次迈出一大步的方式,而不是多次小步的方式。通用的系统能够获得来自不同地区技术资源的全球化的支持。” 这是一种非常适合SEW模式的获得技术发展的途径,Curtin说道。“我们的产品是模件化的,而且我们在全球制造同样的产品,用于发展客户的解决方案。一旦我们理解了用户需要一个解决方案怎样工作并且对这种解决方案的设计和工程进行过细致的优化,然后我们就可以针对这个客户的需求重复使用这种解决方案,还可以把它用于其它地方的有类似要求的客户。这是一种经过标准化的灵活解决方案。”由于这种一体化的传动控制系统已经在实践当中得到证明,SEW公司这种方法也在汽车行业的其它GM公司的竞争者那里得到了应用。 |